Uma logística de entrega organizada e eficiente requer estratégias que mantenham os processos alinhados com o planejamento da empresa para obter resultados positivos. E o picking é uma opção para que a cadeia logística seja executada com agilidade, otimizando o tempo da entrega final.
Hoje, quero falar com você sobre as diferentes etapas e modelos do picking, desde a preparação até a execução e a otimização. Vou explicar quais são os principais modelos e as estratégias mais eficazes para realizar o picking de forma rápida e precisa, minimizando erros e garantindo a satisfação do cliente. Confira!
O que é picking?
Também conhecido como order picking, o picking é a logística que uma empresa utiliza, em seu armazém ou estoque, para despachar o pedido do cliente. Esse processo engloba a localização do produto – assim que a compra é efetuada -, a coleta, a separação, a preparação e a entrega dentro do prazo.
O picking auxilia na melhor organização, padronização e eficiência de cada etapa que envolve a entrega do pedido. Dessa forma, a empresa consegue minimizar erros que possam prejudicar a cadeia logística.
Quais são as vantagens do picking?
O picking é uma ótima estratégia para a empresa que deseja melhorar a organização e a eficiência do seu processo logístico. Assim, é possível oferecer entregas com prazos melhores e, consequentemente, melhorar a satisfação do cliente final.
Um relatório de 2022 realizado pela Capterra mostrou que, para 49% dos entrevistados, o fator mais importante em uma compra online é o tempo na entrega do produto. Isso mostra como a agilidade no processo logístico é essencial para se destacar no mercado e fidelizar o consumidor.
A propósito, a fidelização de clientes é um dos maiores benefícios de implementar o picking, mas ele também oferece outras vantagens para o negócio, como:
- Aumento da produtividade;
- Otimização no tempo de entrega;
- Diminuição de falhas;
- Redução de gastos;
- Melhora na gestão de estoque.
Os modelos de picking
Existem vários modelos de picking para implementar em uma empresa. Assim, é possível avaliar qual é o mais adequado para as necessidades e o planejamento do negócio. A seguir, explico quais são eles e suas principais características.
Picking modelo discreto
O picking modelo discreto é o menos produtivo de todas as opções. O pedido completo é entregue ao separador, que, em seguida, separa cada um dos itens e leva para a doca de expedição.
Mas por que esse modelo é considerado de baixa produtividade? Porque, no modelo discreto, o separador caminha muito e percorre mais distâncias, gerando uma baixa produtividade e uma demanda maior de tempo nessa etapa do processo, já que ele tem um armazém todo para buscar os produtos.
Picking separação por zona
O picking separação por zona diminui os problemas de produtividade do modelo discreto, pois ele tem um separador para cada “rua” do armazém. Um colaborador fica na “rua” A, outro na “rua” B, um para os refrigerados e um para determinados grupos de produtos, de modo que nenhum deles precisa andar o local inteiro.
Se a empresa tem um pedido com vários itens, que estão em zonas distintas, cada separador recebe somente o pedido que diz respeito à sua “rua”, ao seu espaço físico. Ao separá-los, ele os leva em seguida para a doca de expedição.
Na doca de expedição, existe um segundo processo, que é o de agregação desses produtos em um único pedido ou de separação para colocar no caminhão, de modo que depois seja entregue adequadamente.
Esse processo é mais produtivo porque o seu separador percorre uma menor distância e está restrito a apenas uma área do armazém.
Picking por lote
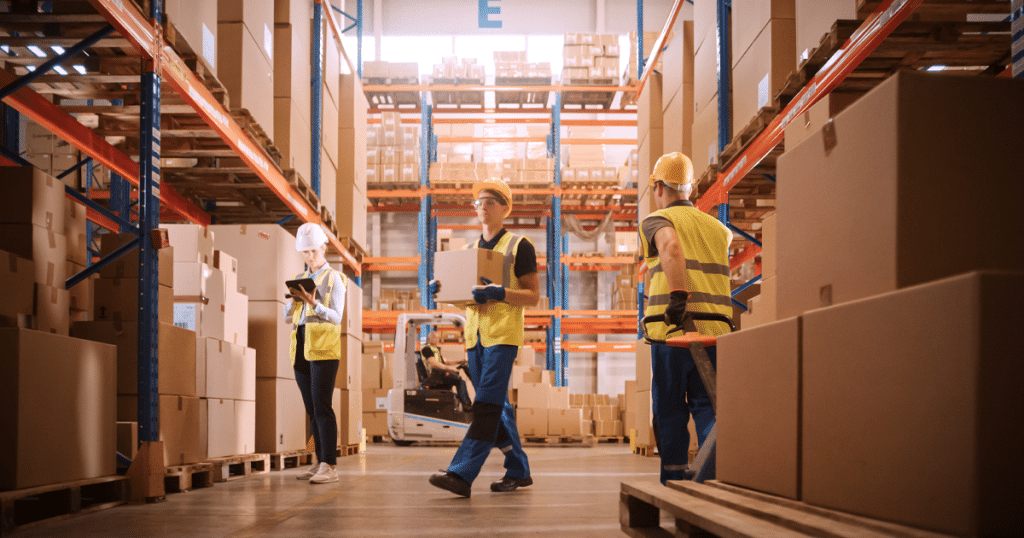
O picking por lote ocorre quando o separador precisa separar um produto específico que não está restrito a uma zona. Em um pedido que tem 10 itens, por exemplo, a empresa solicita 10 tarefas para 10 colaboradores diferentes. Assim, cada um fica encarregado de uma demanda e a empresa consegue agregar vários pedidos.
Uma carga X vai para Brasília, por exemplo, e o cliente A solicita 10 produtos, o cliente B deseja 20 e o cliente C solicita 50. Ou seja, a carga inteira – que vai fazer 20 entregas – tem um total de 300 unidades deste item X.
Com isso, o colaborador encarregado precisa separar os 300 produtos e levar para a doca de expedição, onde será feito o processo de transformar tudo isso em cada um dos pedidos.
Picking por onda
No picking por onda, a empresa avisa o que precisa ser separado, prioriza as tarefas e os separadores executam cada uma de acordo com as prioridades.
Ou seja, são feitos primeiro os pedidos mais urgentes e vão seguindo a ordem até que tudo seja finalizado. É uma maneira menos restrita do que a separação por lote ou a separação por zona.
Picking flow hack
O picking flow hack é quando o armazém possui uma esteira em que as caixas passam e o colaborador vai colocando os produtos. Esse modelo pode ser considerado uma forma de separação por zona, pois cada separador fica encarregado de colocar na caixa os itens relacionados à sua sessão de responsabilidade.
Por exemplo, uma drogaria comprou 600 produtos de diferentes modelos e quantidades. Com o picking flow hack, uma caixa vai passando na esteira e o separador coloca os respectivos itens que fazem parte da sua zona. Ao finalizar, a caixa segue para o próximo funcionário e segue assim até que todos os pedidos estejam juntos.
Gostou deste conteúdo? Então, inscreva-se no canal do Mestre do ERP para acompanhar mais assuntos como esse e compartilhe sua experiência nos comentários.
Aproveite também para assistir ao vídeo em que falei sobre o assunto.